L'équipement d'origine, c'est nous
Chaque pièce détachée Lemförder passe par un processus de développement long et complexe avant d'entrer sur le marché. Puisque nous travaillons directement avec les fabricants OE, nous sommes conscients de notre responsabilité et nous vous assurons que chaque pièce passe les tests et répond aux exigences OEM. Immiscez-vous dans notre département Développement et vous comprendrez comment nos nombreuses années d'expérience en équipement d'origine et notre expertise de pointe font toute la différence.
Développement de LEMFÖRDER
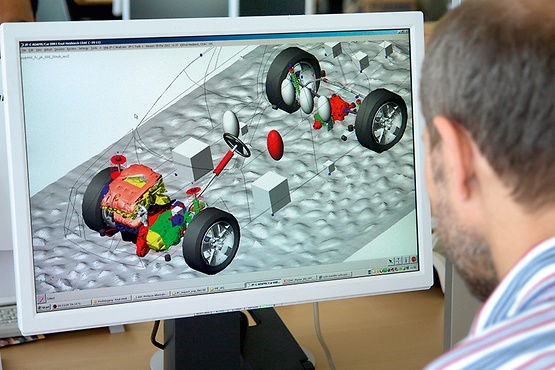
Recherche et développement
La conception préliminaire sur écran marque le départ du développement d'une pièce de châssis. Nos ingénieurs expérimentés déterminent, en collaboration avec les fabricants du véhicule, les exigences matérielles, la géométrie, le design et la configuration des points de montage pour chaque pièce développée. Dans le processus, nous ne prêtons pas seulement attention au fonctionnement individuel des pièces, mais nous vérifions également que celles-ci fonctionnent correctement ensemble. Les attentes concernant les forces d'action et l'espace de montage disponible sont aussi prises en compte, ainsi que l'interaction entre les pièces du châssis directement connectées. Le fabricant du véhicule indique ces paramètres dans les spécifications.
Les premières simulations informatiques, par exemple les analyses par méthode des éléments finis (MEF), sont ensuite effectuées. Une fois ces simulations passées avec succès, le processus de conception se poursuit avec l'étape suivante qui implique la construction des premiers prototypes.
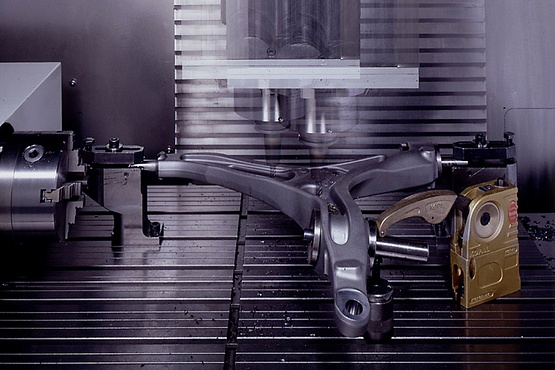
Concevoir le prototype
Les premiers prototypes sont souvent passés au crible. Les modélisations 3D proposées par le département Développement sont préparées conformément à l'usinage sur machine CNC.
Ici, la créativité et la précision absolue sont à l'ordre du jour.
Ce qui, jusqu'ici, n'existait que virtuellement à l'intérieur de l'ordinateur est maintenant réel et tangible.
Après la validation de la pièce, la prochaine étape implique la production de petites quantités de pièces à partir d'outils similaires aux véritables outils de production (par exemple, de faux bras de suspension).
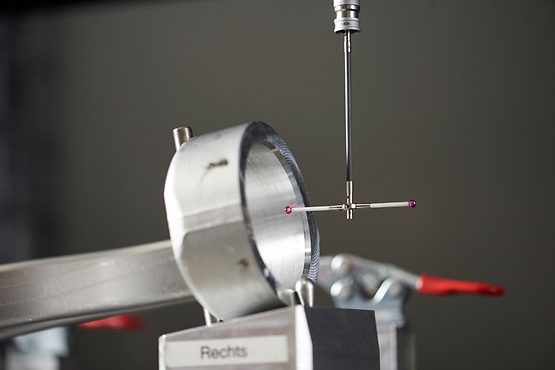
Toutes les pièces détachées et les pièces de châssis préassemblées sont mesurées, les caractéristiques matérielles analysées et toutes les valeurs fonctionnelles vérifiées et listées dans les spécifications.
Les prototypes sont ensuite testés en laboratoire ou sur des véhicules test jusqu'à ce qu'ils correspondent enfin aux exigences et aux souhaits du fabricant.
C'est ainsi que plus de 15 000 prototypes sont produits chaque année.
Pour assumer les coûts associés à cette production, il faut une entreprise renommée et prospère depuis plusieurs années sur le marché.
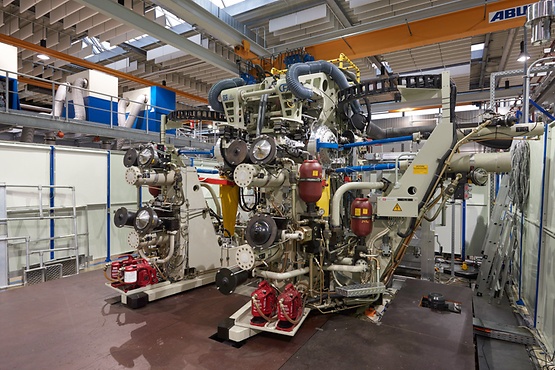
Test et validation
Nous garantissons une qualité optimale et nous respectons cet engagement grâce à différentes procédures de test qui dépassent de loin les normes habituelles du marché. Outre les études poussées dans nos locaux de recherche et développement, tous les produits LEMFÖRDER sont soumis à des essais de charge extrêmes en situation réelle. Les facteurs essentiels suivants sont vérifiés :
- Couple de démarrage
- Couple de rotation et de basculement
- Flexibilités radiale et axiale
- Résistance à l'arrachement et à la compression du pivot à rotule
- Résistance au flambage
Si certaines valeurs ne correspondent pas aux niveaux de tolérance exigés, le confort de l'utilisateur peut être considérablement compromis. Les variables physiques observées fournissent aussi un aperçu de l'usure et de la sûreté des pièces testées.
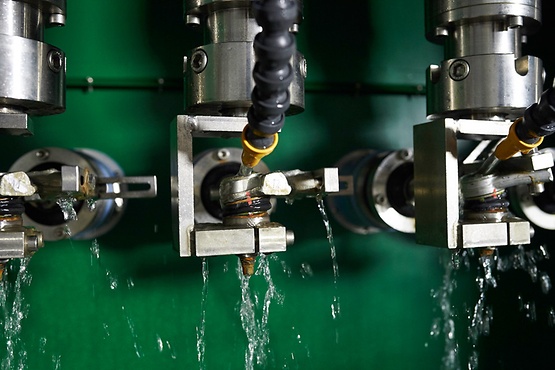
Les exigences techniques pour ces pièces sont devenues de plus en plus pointues au cours des dernières années. Ceci influe à la fois sur les méthodes de test et sur leur durée. Les tests sont plus nombreux et plus longs. Les exigences imposées aux produits sont aussi considérablement plus élevées du fait de la mondialisation des marchés.
Par exemple, le scellement des pièces est testé en simulation environnementale à des températures allant de -40 °C à +100 °C. Outre l'eau pure, de l'eau salée ou une solution salée concentrée est également utilisée lors des tests.
En parallèle, les pressions exercées lors du lavage d'un véhicule (approximativement 10 bar) et dans une laveuse à pression (jusqu'à 100 bar et 80 °C pour la température de l'eau) sont également simulées.
Le système doit non seulement résister à la pression de l'eau, mais aussi être solidement connecté mécaniquement afin que la pression de l'eau ne puisse pas desceller le soufflet d'étanchéité.
Par conséquent, chaque pièce LEMFÖRDER est certifiée selon les normes ISO/TS 16949 et (UE) n° 461/2010.
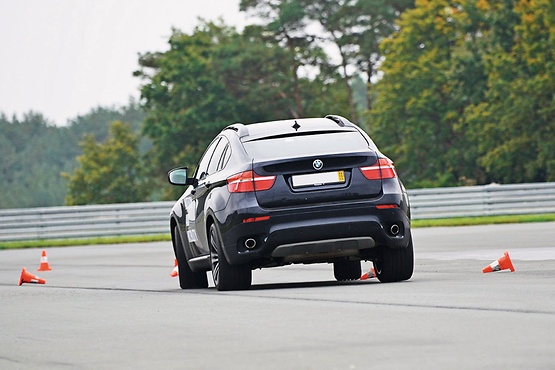
Test de conduite
Après validation sur le banc d'essai, l'étape finale du développement consiste à effectuer l'essai sur route sur les pistes du fabricant automobile, spécialement conçues pour tester le véhicule avant sa sortie.
Les pièces sont soumises à des tests intensifs de conduite dans des conditions de route et climatiques variées.
Toutes les situations de conduite envisageables, toutes les surfaces de route possibles et les différents styles de conduite sont considérés.