Despite the increasing number of vehicles with disc brakes on the rear axle, drum brakes remain a fixed component of vehicle engineering. Driving dynamics systems such as ABS and VSC have not changed this either – both systems also work with drum brakes.
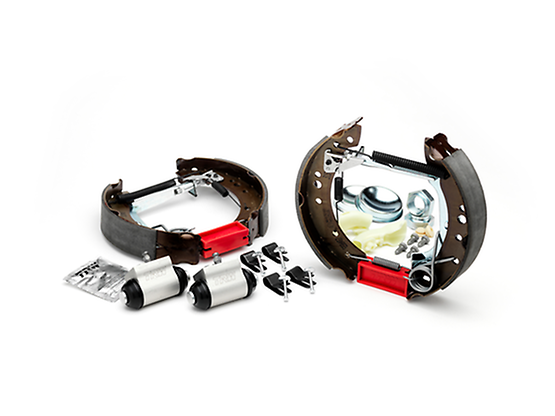
The main prerequisite for this is a well maintained drum brake with all individual components in full working order. But in practice, this is also where the problems often start. This is because often when the brake shoes and the wheel cylinder are changed, not enough attention is paid to the other parts of the system. And yet, it is precisely the pull-off springs, shoe steady springs and the adjuster which are crucial for the reliable functioning of the driving dynamics systems. The TRW-Superkit can help with this – it includes all these parts. That means no worn components have to be re-used. Let us take a closer look at these components.
How-to-guide
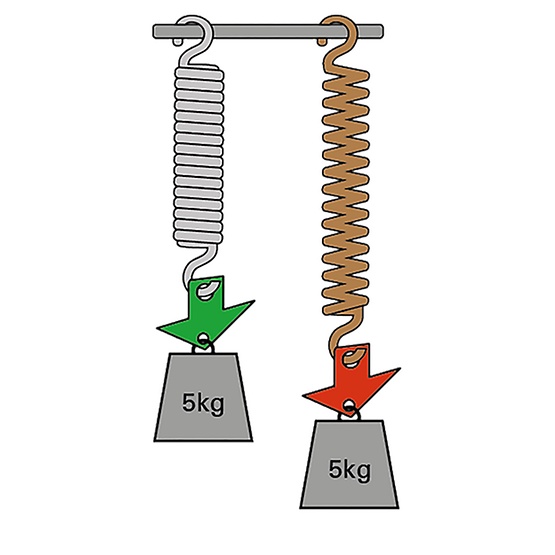
As the brake shoes have to be mechanically pulled back into their starting position after a braking procedure, the tensile force of the pull-off springs is of particular importance. Over time, however, these springs lose elasticity. This results in a grinding brake and – as a result – noise and permanently excessive operating temperatures. Because the maintenance interval for drum brakes is two to three years on average, we absolutely recommend replacing the springs.
Wear on pull-off springs
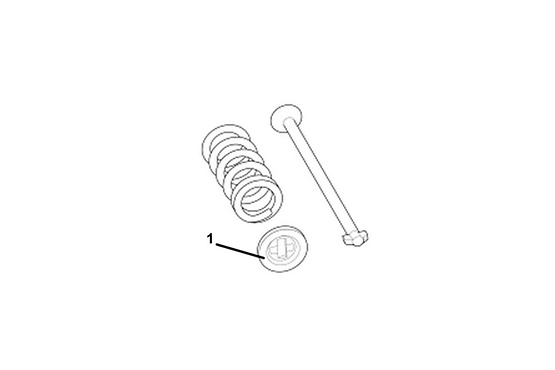
The same applies the brake shoe steady springs. In addition to the decreasing spring action, the lock plates (fig. 1: 1) are particularly susceptible to corrosion damage. If the shoe steady spring comes loose due to a lock plate coming off, this can have severe consequences: the brake shoe slides over the piston of the wheel cylinder, pushing it completely out of its housing – the brake fails completely.
Fig. 1 Shoe steady spring with lock plate
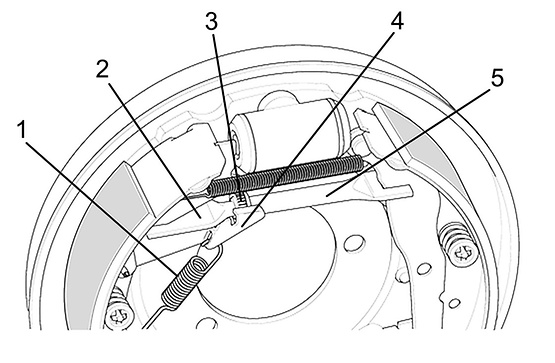
With increasing wear of the friction material, the mechanical adjuster units of the drum brake systems adjust the brake shoes. There is a large number of different systems. This article only looks at the system of so-called incremental adjustment. The adjuster with pinion consists of the threaded pressure rod (fig. 2: 2), the adjusting pinion (fig. 2: 3), the compression sleeve (fig. 2: 5), the adjusting lever (fig. 2: 4) and a spring (fig. 2: 1) The adjusting lever (fig. 2: 4) is rotatably mounted in the brake shoe and meshes into the adjuster pinion (fig. 2: 3) with an angled edge. When the service brake is operated, the brake shoes are pushed apart by the wheel cylinder pistons. If the air gap becomes larger than the design air gap due to wear of the lining, the adjustment pinion (fig. 2: 3), is rotated around a tooth flange with the adjuster level (fig. 2: 4) by one tooth flank so the threaded pressure rod is screwed out. This makes the entire adjuster unit longer, establishing the design air gap again. The spring (fig. 2: 1) provides the adjustment moment here.
Fig. 2 Adjuster unit with pinion
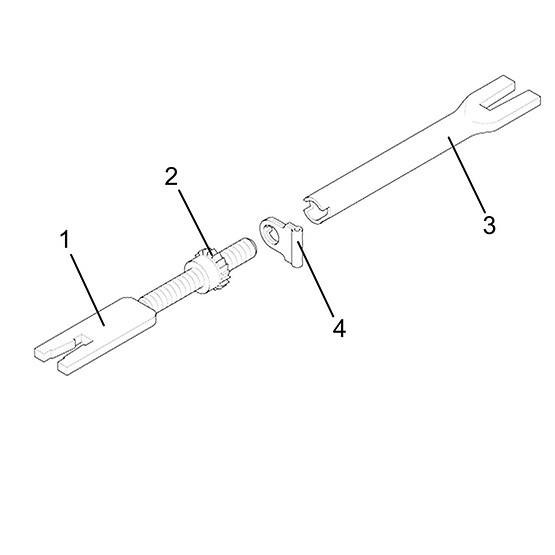
Fig. 3 Adjuster unit with thermo-clip
When the brakes are put under great stress (thermal strain) the brake drum expands (the diameter of the drum increases), in turn increasing the air gap between drum and lining material. To avoid adjusting the brake into the “hot drum”, this adjustment unit is equipped with a thermo-clip (fig. 3: 4; fig. 4: 4). The thermo-clip is located between the adjustment pinion (fig. 3: 3) and the compression sleeve (fig. 3: 1) With increasing brake temperature, the drum expands and proportionally with it the thermo-clip as well.
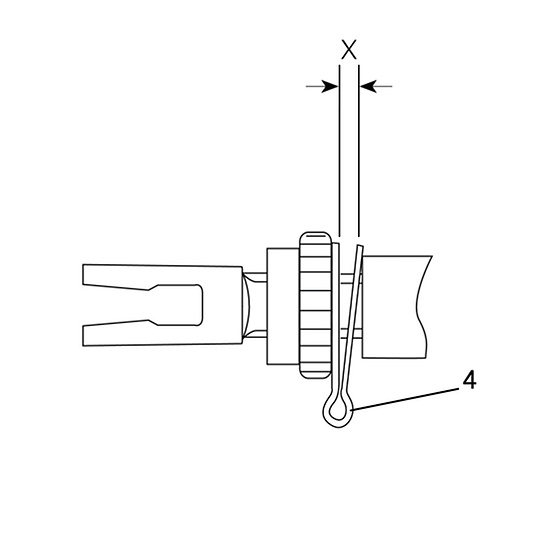
Fig. 4 Function of the thermo-clip
The entire adjustment unit is lengthened by dimension “X” (fig. 4), avoiding undesired adjustment. It returns to the original state after the brake or the thermo-clip have cooled down.
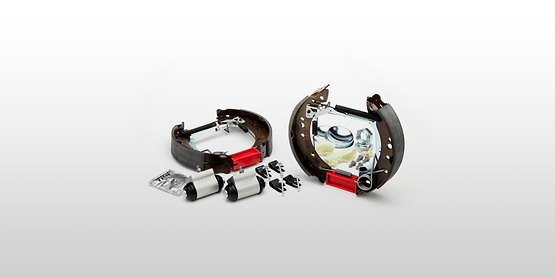
If only the shoes and the wheel cylinders are replaced during a repair of the drum brake, a residual risk remains for the reliability of the remaining components. If part of the adjuster unit turns out to be defective during the repair, this can also lead to unpleasant surprises: the required spare parts can then usually only be acquired from the dealership workshop, which is expensive and time-consuming. The advantages of the Superkit are therefore obvious: not only does it speed up the repair process significantly, it is also always safer than replacing only individual parts.
Superkit – fast and easy repairs
Nice-to-know
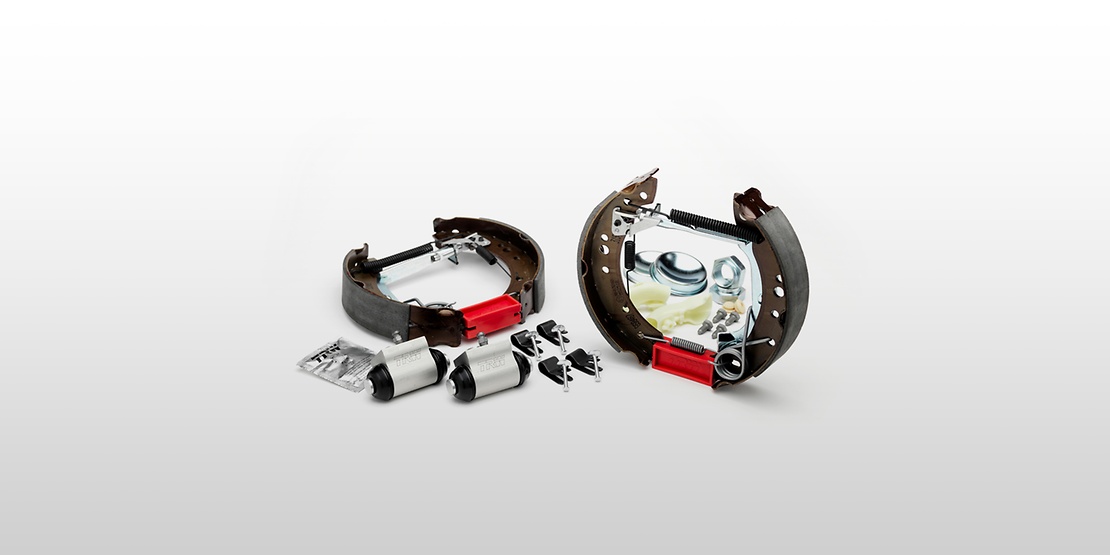
ZF Aftermarket product range
Discover the complete portfolio of brakes in our product catalog.