Reduce the friction torque on disc brakes - without any electronics
Discussions focusing on reducing fuel consumption and the associated CO2 emissions as well as minimizing noises in the increasingly growing number of electric vehicles in the future are matters of urgency concerning vehicle manufacturers. One step in this direction is the development of the active pad retraction mechanism – a minor component with a major effect.
How-to-guide
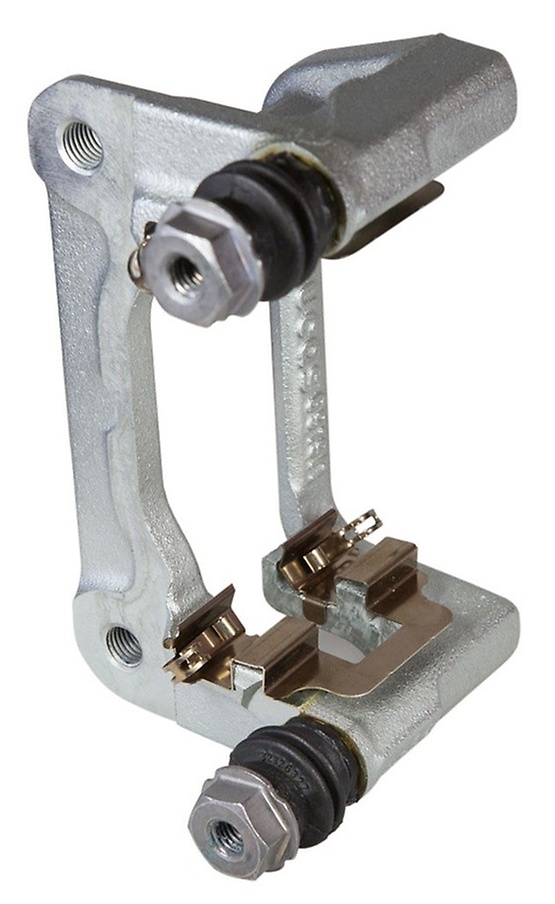
When braking, the vehicle's kinetic energy is converted into heat energy. This is caused by the brake pads pressing on the brake discs to decelerate the vehicle. After the braking action, when the brake is released, the brake pads have to return to their original position. For wear and noise characteristics, it is particularly important that this is done with minimum residual friction torques, whenever possible. On the other hand, however, the brake pad may not be too far apart from the brake disc as otherwise the pedal travel and the brake response time would enter a safety-critical state. This compromise has always presented engineers with diverse challenges.
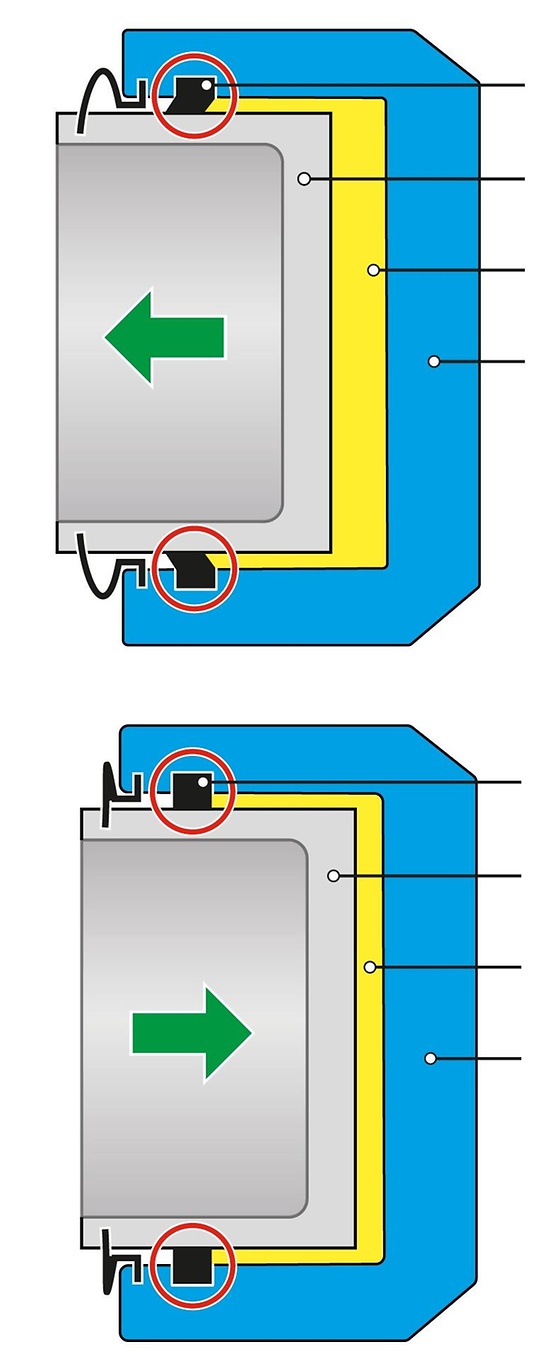
In contradiction to the widespread yet ultimately false assumption that the pads are returned to their starting position by a lateral run-out of the brake disc, this is actually done with the help of the sealing rings of the brake caliper piston.
When the piston is displaced (brake actuated), the static friction of the sealing rings causes them to move and warp slightly (elastic) (Fig.1). Once the brake has been released, the pressure in the brake caliper reduces to zero and the pre-stressed (warped) sealing rings pull the pistons back to their original position (Fig. 2). This maintains the running clearance (determined by the design) between the brake disc and pads.
Since the piston displacement force is greater than the static friction force of the sealing ring when the pad wear increases, the piston slides through the sealing ring to the same amount as the pad wear. Once the brake is released, the running clearance defined by the design is restored thanks to the rollback effect.
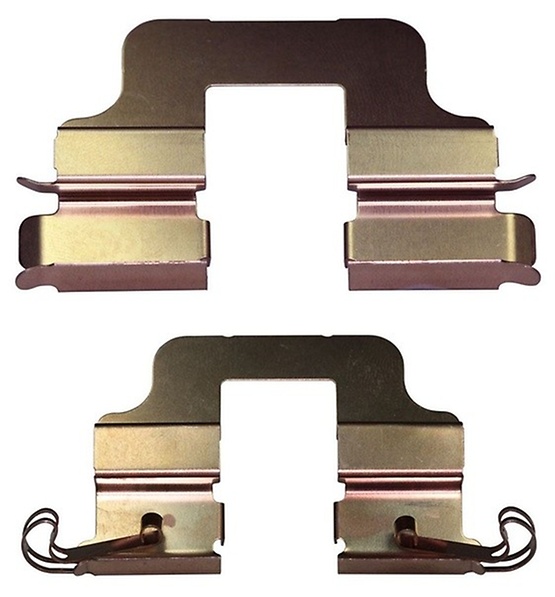
Since the design sometimes restricts the pad from retracting along the piston sealing, it was necessary to find a supportive solution to this problem. The result of this development project was the design of an active brake pad retraction mechanism.
The residual slip torque has to be measured on the wheels which show resistance during rotation. To do this, remove the cover in the rim to access the axle nut below.
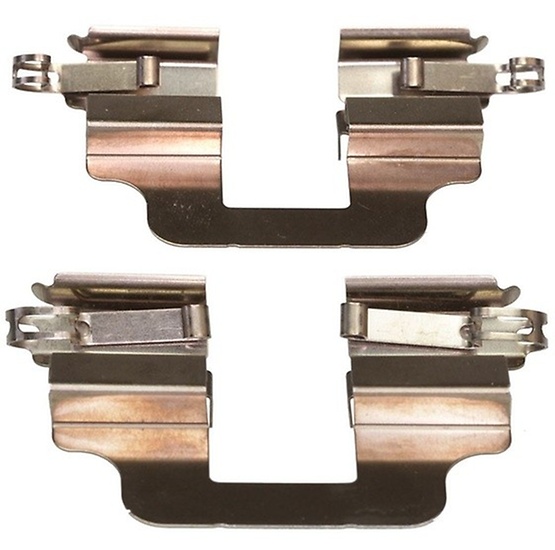
The active brake pad retraction mechanism is a further development of the pad retaining springs designed to improve pad retraction. The springs were upgraded by the attachment of an additional spring mechanism which not only improves the sliding of the pad lugs on the carrier, but also retracts the pad away from the brake disc.
During the course of the brake pad's service life, the spring elongates accordingly to guarantee safe and reliable functioning even when the pad wear increases.
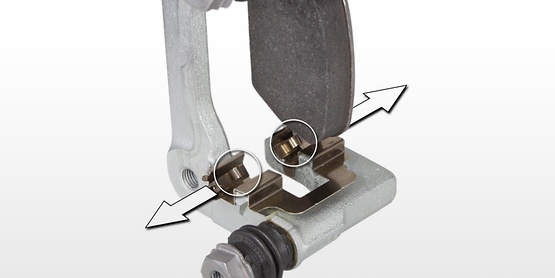
To ensure the safe functioning of this system, the springs must be replaced every time the pad is changed. Over time, a used spring has adapted its length to the pad wear and can no longer function correctly with a new pad.
When new brake pads are fitted, it is important to make sure that the pad lugs are positioned correctly to the spring bar so that the spring retracts the pad from the brake disc after braking.
Nice-to-know
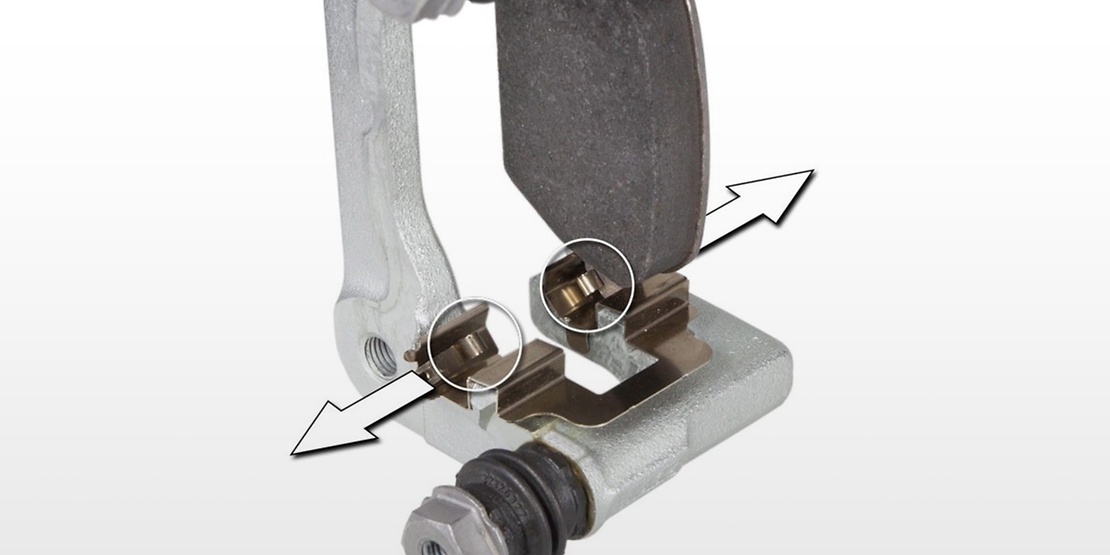
ZF Aftermarket product range
Discover the complete portfolio of brakes in our product catalog.