我々はOEを理解している - なぜなら我々はOEだからだ
Lemförderの各スペアパーツは、市場に出るまでに長く複雑な開発プロセスを経ています。私たちはOEメーカーと直接仕事をしているため、一つ一つの部品が彼らのテストに合格し、OEMの要件を満たしていることを保証する責任を自覚しています。当社の開発部門をご覧いただければ、当社の数十年にわたるOE経験と最先端の専門知識が、なぜすべての違いを生み出すのかがおわかりいただけるでしょう。
レムフォルダーの開発
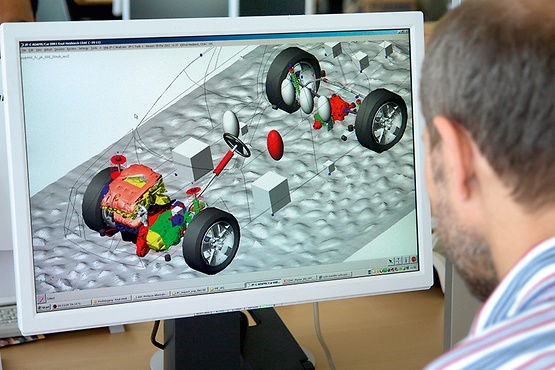
研究開発
画面上の予備設計が、シャーシコンポーネントの開発をスタートさせます。当社の経験豊富なエンジニアは、車両メーカーと協力しながら、開発する各部品の材料要件、形状、設計、取り付け箇所の構成を作成します。このプロセスでは、個々の部品の機能に注意を払うだけでなく、部品が互いに正しく機能するかどうかもチェックします。作用する力や利用可能な取り付けスペースに関する予想される要件も、直接接続されたシャーシ部品との相互作用とともに考慮されます。次に、FEM強度解析などの最初のコンピュータ・シミュレーションが実行されます。これらが成功裏に完了すると、設計リリースは、初期プロトタイプを製作する次のステップに進みます。
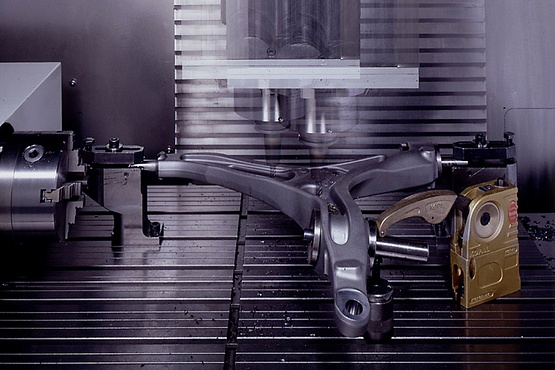
プロトタイピング
最初のプロトタイプは通常、ソリッドブロックから削り出される。開発部門から提供された3Dモデルは、CNC加工用に準備されます。ここでは、絶対的な精度と結合した創造性が一日の順序です。
これまではコンピュータの中にバーチャルに存在するだけだったものが、現実の具体的なものに変わるのだ。部品がリリースされると、次の段階では、生産に近いツール(鍛造コントロールアームなど)から少量生産が行われる。
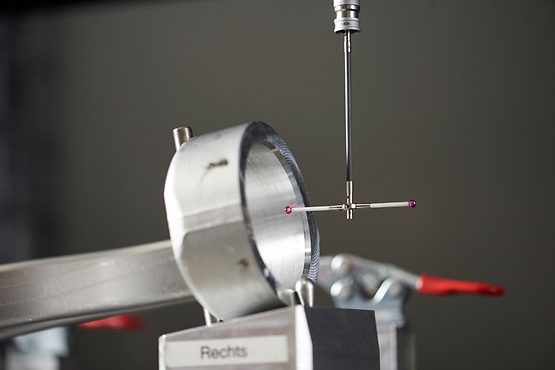
個々の部品と組み立て済みのシャーシ部品はすべて測定され、材料特性が分析され、すべての機能値がチェックされ、要求仕様書に従って文書化されます。
プロトタイプはその後、実験室やテスト車両でテストされ、最終的に自動車メーカーの要求や希望に沿うものに仕上がる。こうして、年間15,000台以上のプロトタイプが生産される。
関連コストを負担するには、長年にわたって市場で成功を収めてきた有名企業が必要だ。
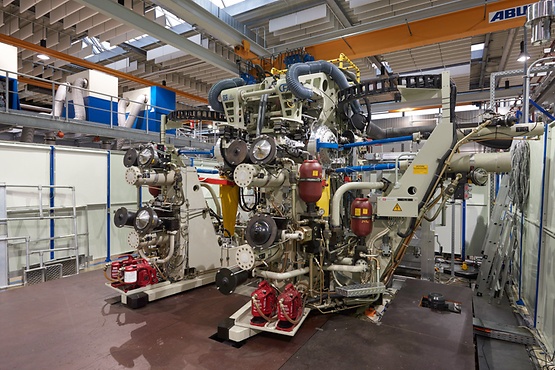
テストと検証
LEMFÖRDERは、市場で通常見られる基準をはるかに超えるさまざまな試験手順を通じて、最大限の品質への自主的な取り組みを実現しています。LEMFÖRDERの全製品は、研究開発施設での広範な研究に加え、実際の条件下で集中的な負荷試験を受けています。以下の重要な要素がチェックされます:
- 離脱トルク
- 回転・傾斜トルク
- ラジアル弾性とアキシャル弾性
- ボールスタッドの引き抜きと押し出し強度
- 座屈力
ある測定値が必要な許容範囲から外れると、快適性が著しく損なわれる可能性が高い。また、観測された物理的変数は、試験された部品の摩耗や安全性についての洞察も与えてくれる。
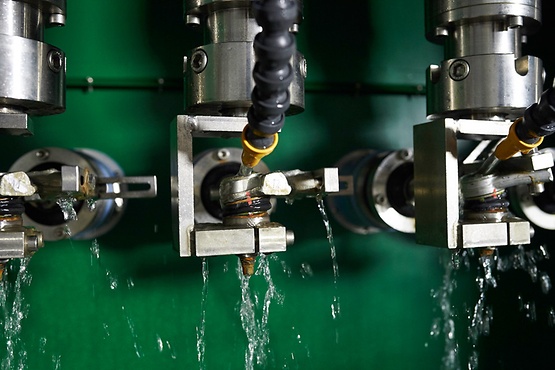
これらの部品に対する要求は、ここ数年で大幅に高まっている。それは、試験方法と試験期間の両方に影響する。より多くの、より長い試験が実施されている。また、市場のグローバル化により、製品に求められる要件も大幅に増加している。
システムは、一方では水圧に対して密閉されていなければならないが、他方では、水圧でシーリングブーツが外れないように機械的にしっかりと接続されていなければならない。
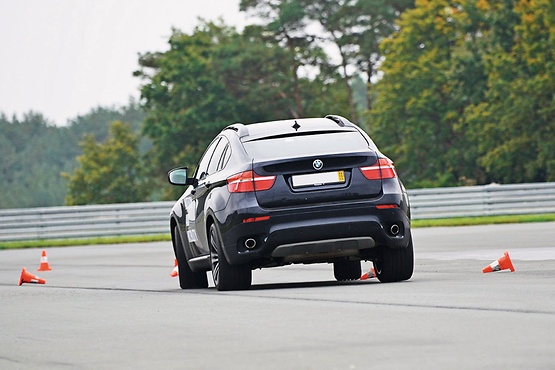
運転免許試験
テストベンチでの検証の後、開発の最終段階として、自動車メーカーの発売関連テストコースでの走行テストが行われる。
そのため、部品は最も過酷な気象条件や作業負荷のシミュレーションを含む、あらゆる種類の道路状況下でテストされている。
このようにして、レムフォーダーのすべての部品が、OEMの最高基準を満たし、優れたグリップとスムーズなドライビングダイナミクスを実現するための厳しい基準を満たすようにしています。言い換えれば、安全性と快適性の完璧な組み合わせを見つけることです。